Programmable light stick with the Raspberry Pi Pico
Painting with Light
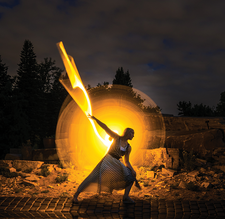
© Photo by Xuan Nguyen on Unsplash
In the photographic method of light painting, you expose a subject over an extended period of time while moving the light sources. With a little technical support from a Raspberry Pi Pico, you can achieve sophisticated results.
Without light, nothing can be seen in photography, but with just a little background light and light brushes, you can create interesting motifs. For long exposures, you need a camera with manual adjustment and a tripod. A flashlight or laser pointer is sufficient to paint simple patterns or lettering into an on-going exposure. If you like to experiment, you might want to work with LEDs to achieve particularly interesting light graphics.
I was interested in a creative approach and in trying out what can be achieved with modern pixel elements and clever programming. The idea of a light stick for light painting was born. In this article, I use a Raspberry Pi Pico to build a MicroPython programmable LED light stick.
The control does not require much in the line of interfaces, and the hardware needs to be as compact as possible – a good fit for the Pico, which is the youngest member in the Raspberry Pi family and has already seen a huge amount of interest in the last months, with some interesting HATs to match. The large community proves to be a boon if you are looking for help. Currently the smallest Raspberry Pi model, the Pico comes with an RP2040 microcontroller chip and an ARM Cortex M0+ processor, offering a state-of-the-art alternative to comparable controllers. It can run C/C++ and performs well with MicroPython.
[...]
Buy this article as PDF
(incl. VAT)
Buy Linux Magazine
Subscribe to our Linux Newsletters
Find Linux and Open Source Jobs
Subscribe to our ADMIN Newsletters
Support Our Work
Linux Magazine content is made possible with support from readers like you. Please consider contributing when you’ve found an article to be beneficial.
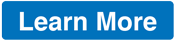
News
-
Fedora Continues 32-Bit Support
In a move that should come as a relief to some portions of the Linux community, Fedora will continue supporting 32-bit architecture.
-
Linux Kernel 6.17 Drops bcachefs
After a clash over some late fixes and disagreements between bcachefs's lead developer and Linus Torvalds, bachefs is out.
-
ONLYOFFICE v9 Embraces AI
Like nearly all office suites on the market (except LibreOffice), ONLYOFFICE has decided to go the AI route.
-
Two Local Privilege Escalation Flaws Discovered in Linux
Qualys researchers have discovered two local privilege escalation vulnerabilities that allow hackers to gain root privileges on major Linux distributions.
-
New TUXEDO InfinityBook Pro Powered by AMD Ryzen AI 300
The TUXEDO InfinityBook Pro 14 Gen10 offers serious power that is ready for your business, development, or entertainment needs.
-
Danish Ministry of Digital Affairs Transitions to Linux
Another major organization has decided to kick Microsoft Windows and Office to the curb in favor of Linux.
-
Linux Mint 20 Reaches EOL
With Linux Mint 20 at its end of life, the time has arrived to upgrade to Linux Mint 22.
-
TuxCare Announces Support for AlmaLinux 9.2
Thanks to TuxCare, AlmaLinux 9.2 (and soon version 9.6) now enjoys years of ongoing patching and compliance.
-
Go-Based Botnet Attacking IoT Devices
Using an SSH credential brute-force attack, the Go-based PumaBot is exploiting IoT devices everywhere.
-
Plasma 6.5 Promises Better Memory Optimization
With the stable Plasma 6.4 on the horizon, KDE has a few new tricks up its sleeve for Plasma 6.5.