An inexpensive open source 3D printer
Open Hardware – Printy
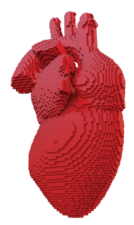
© Lead Image © Kirill Cherezov, 123RF.com
Printy offers an inexpensive, open source DIY 3D printer kit, with a license that paves the way for future open source solutions.
If a single technology defines crowdfunding and open hardware, it would be 3D printing. Not only did 3D printers appear at about the same time as crowdfunding and open hardware, but the demand for cheaper 3D printers has always been high. Even more importantly, 3D printers are a way for other open hardware projects to print cases and replacement parts, overcoming the problems of manufacturing hardware. Kickstarter alone lists 685 projects related to 3D printing over the last decade – however, most are proprietary, only 37 are open source and even those may use obsolete technologies [1]. Jay Lin's Printy project [2] is an attempt to bridge that gap with an inexpensive do-it-yourself open hardware kit (Figure 1) whose crowdfunding campaign will be underway by the time this magazine hits the newsstands.
Printy's Crowd Supply page spells out the current situation: "SLA [Stereolithography] 3D printers are not only expensive, they are typically proprietary. For an enthusiast trying to find the right balance between low cost, high print quality, and open source design, the best advice one could offer has long been 'pick one'. The current market has left the 3D printer community stranded in a disconnected ecosystem full of walled gardens. With Printy, we aim to dismantle those walls and help reconnect that community. And what better way to share the joy of 3D printing than by first sharing the joy of building a 3D printer?"
Lin discovered both open source and 3D printers through RepRap [3], a project to build an affordable 3D printer that began in the UK in 2005. "The idea of printing any object was appealing," he says. "I purchased a Printrbot kit [4], as it struck the right balance between cost and performance. The assembly was great, and I learned a lot about Fused Deposition Modeling (FDM) printers [an obsolete printing technique, 5] via the construction process. That is when I realized that a majority of the joy came from learning about how the printer works rather than what can be printed. Thus, the seeds of Printy were planted. The idea was to make a [modern] Stereolithography (SLA) kit printer [6] to share the joy of construction and learning about this next level of 3D printer technology." In other words, Lin's goal is to build a high resolution 3D printer whose output matches the quality of top-of-the-line proprietary ones.
Coming relatively late into the 3D printer market, Lin was able to learn from the mistakes of others. In particular, Lin was struck by Peachy Printer's [7] crowdfunding campaign. In September 2013, Peachy Printer raised over $650,000 in its campaign to build a $100 3D printer. However, after countless delays, in 2016, the developer was forced to admit that his partner had embezzled $320,000 of the funds raised, putting an end to the project and leaving backers with neither their money nor a printer. Peachy Printer was not the first 3D printer project to collapse – nor even the first crowdfunding campaign to renege – but its size, as well as the initial enthusiasm for it, devastated the development community, including Lin. "I watched my friends' investments into Peachy Printer vaporize in a spectacular way," Lin says. "Since Printy was already in the design phase, I made sure to focus on completing the product before anyone else risked a dime."
Lin continues, "To further reduce buyer's risks, I made use of standard components wherever possible, including the NEMA 17 stepper motor, 8mm linear rails, bearings, endstop switches, Arduino board, and metric screws [Figure 2]. In case any part breaks or goes missing, those components can be easily sourced. A buyer who has all the common components should only need to purchase a few unique components instead of the whole product. Moreover, a hobbyist with access to advanced tools such as laser cutters, soldering equipment, and sheet metal equipment should be able to make those unique components."
To help users, Lin is keeping the bills of materials as spreadsheets on GitHub [8] (Figure 3). The spreadsheets are literally a piece-by-piece inventory of the hardware and tools required to construct a Printy, detailing screws, Allen wrenches, zip ties, safety goggles, and everything else. The last column in each row of the spreadsheets adds exact sizes, as well as advice like "Try to source from the same vendor" – a precaution that could eliminate minute differences in the sizes of the components. The spreadsheets end with images of the components in order to minimize the possibility of confusion.
The build instructions [9] are similarly comprehensive (Figure 4). Although I have worked extensively as a technical writer in my time, it is no exaggeration to say that I have never encountered such a thorough set of instructions, even among those written by professional writers. As Lin notes, assembling a Printy includes such key steps as "the placement of the laser and a series of mirrors to guide the laser beam into 2D patterns. To create the third dimension, there is a platform that traverses up and down along a linear rail." All these steps require precision, a fact that is reflected in the instructions.
Printy Specs and Licensing
Table 1 shows Printy's basic specifications as listed on CrowdSupply. These specifications are a trade-off with the cost. For example, the print dimensions are relatively small compared to other SLA printers. Similarly, the resolution is about half and the speed about a quarter those of top-of-the-line proprietary printers.
Table 1
Printy Specifications
Hardware license |
CERN OHL v1.2 |
Software |
Based on Marlin firmware, licensed under the GNU GPL |
Print dimensions (X x Y x Z) |
110x110x150mm |
Resolution (X, Y, and Z) |
50 microns |
Maximum speed (X & Y) |
> 600mm/s |
The finished product documentation will explain how the skilled and adventuresome can go beyond Lin's design. Lin explains that "anyone can scale each dimension of the laser-cutting DXF files and create a Printy Deluxe. By tweaking the schematics, one can substitute the 14-bit DAC with a 24-bit DAC to enable resolutions that will be the envy of industrial 3D printers. [In addition], the firmware can be ported from 8-bit AVR to a more modern 32-bit ARM processor and achieve much faster print speeds. I plan to document the production steps to aid this group of tinkerers so they can focus on experimentation instead of finding shops that can make their variants." For those willing to make the extra effort, the results should equal or perhaps even exceed the top-of-the-line proprietary printers.
These improvements are possible in part because of the use of the CERN Open Hardware Licence (OHL) [10]. The CERN OHL describes itself as being "to hardware what the General Public Licence (GPL) is to software," and, as Lin explains, is intended for "a project that involves mechanical, electrical, and firmware design." Like the GNU GPL, the OHL allows modifications to a project's elements so long as the modifications are released under the same license. Under the terms of the license, any of the modifications of Lin's basic design can become available to others, which justifies Lin's claim that, technically, "Printy compares favorably against much more expensive machines."
Already, the licensing promises one benefit. Printy's firmware is a fork of Marlin firmware, an open source project that is used even for proprietary printers [11]. Printy's innovation is to adapt a stepper-based firmware into a galvanometer-based machine, according to Lin, expanding the license's usefulness.
By itself, Printy promises to be an inexpensive and open source solution for 3D printing. However, its licensing means that future open source solutions can be more easily developed because of what Lin has already done. "Design," as Lin says, "isn't the end of a project. I find the media, manufacturing, and community building aspects to be equally interesting. I would love to connect with anyone who is inspired to modify and create their own Printy. As for my next project, a desktop metal 3D printer is intriguing."
Infos
- Kickstarter 3D printer projects: https://www.kickstarter.com/discover/advanced?ref=nav_search&term=%223D%20printer%22%20%22open%20source%22
- Printy: https://www.crowdsupply.com/alch3my/printy
- RepRap: https://en.wikipedia.org/wiki/RepRap_project
- Printrbot: https://en.wikipedia.org/wiki/Printrbot
- FDM printers: https://en.wikipedia.org/wiki/Fused_filament_fabrication#Fused_deposition_modeling
- Stereolithography: https://en.wikipedia.org/wiki/Stereolithography
- Peachy Printer: https://3dprint.com/133842/peachy-printer-embezzlement/
- Printy's bills of material: https://github.com/alch3my/printy/find/master
- Printy's build instructions: https://github.com/alch3my/printy/blob/master/Mechanical/Instructions/BuildInstructions.md
- CERN OHL: https://ohwr.org/project/cernohl/wikis/home
- Marlin firmware: https://marlinfw.org/
Buy this article as PDF
(incl. VAT)
Buy Linux Magazine
Subscribe to our Linux Newsletters
Find Linux and Open Source Jobs
Subscribe to our ADMIN Newsletters
Support Our Work
Linux Magazine content is made possible with support from readers like you. Please consider contributing when you’ve found an article to be beneficial.
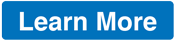
News
-
AlmaLinux OS Kitten 10 Gives Power Users a Sneak Preview
If you're looking to kick the tires of AlmaLinux's upstream version, the developers have a purrfect solution.
-
Gnome 47.1 Released with a Few Fixes
The latest release of the Gnome desktop is all about fixing a few nagging issues and not about bringing new features into the mix.
-
System76 Unveils an Ampere-Powered Thelio Desktop
If you're looking for a new desktop system for developing autonomous driving and software-defined vehicle solutions. System76 has you covered.
-
VirtualBox 7.1.4 Includes Initial Support for Linux kernel 6.12
The latest version of VirtualBox has arrived and it not only adds initial support for kernel 6.12 but another feature that will make using the virtual machine tool much easier.
-
New Slimbook EVO with Raw AMD Ryzen Power
If you're looking for serious power in a 14" ultrabook that is powered by Linux, Slimbook has just the thing for you.
-
The Gnome Foundation Struggling to Stay Afloat
The foundation behind the Gnome desktop environment is having to go through some serious belt-tightening due to continued financial problems.
-
Thousands of Linux Servers Infected with Stealth Malware Since 2021
Perfctl is capable of remaining undetected, which makes it dangerous and hard to mitigate.
-
Halcyon Creates Anti-Ransomware Protection for Linux
As more Linux systems are targeted by ransomware, Halcyon is stepping up its protection.
-
Valve and Arch Linux Announce Collaboration
Valve and Arch have come together for two projects that will have a serious impact on the Linux distribution.
-
Hacker Successfully Runs Linux on a CPU from the Early ‘70s
From the office of "Look what I can do," Dmitry Grinberg was able to get Linux running on a processor that was created in 1971.